outubro 12, 2020
Implementation of Lockout-Tagout in Ludvika, Sweden
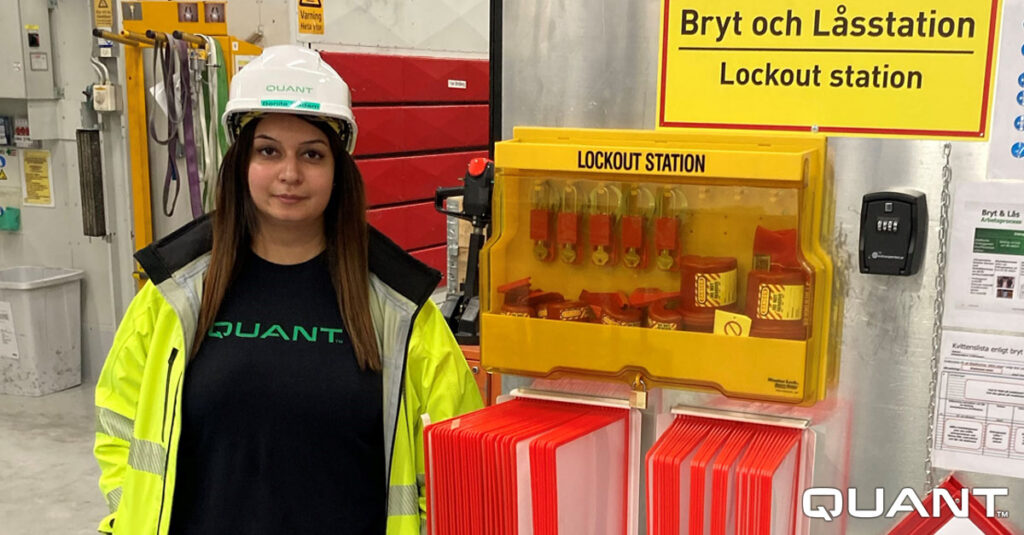
At Quant’s site in Ludvika, Sweden, a project for implementing a lockout-tagout procedure for all areas of the site has been initiated.
Just over halfway through the project, Benita Padam, Quant maintenance engineer in Ludvika, can see several advantages from the implementation, especially from a safety point of view:
“The result from implementing lockout-tagout is that there will be fewer accidents, a safer workplace, and that our safety culture is further strengthened. And there are also many other benefits”.
Quant’s partnership with Hitachi ABB Power Grids in Ludvika goes back to 2006, when the original contract started. Operations at this site includes development and manufacturing of large power transformers and high voltage products, as well as high-voltage direct current systems for grid interconnections, offshore wind connections etc.
A good and safe working environment is an important strategic issue for Hitachi ABB Power Grids. The objective of their working environment activities is to create a physically, psychologically and socially sound and stimulating workplace for all employees, where the risks of occupational injury and work-related ill-health are prevented. Close co-operation with suppliers is a natural way of working in their organization.
Quant started this LOTO project together with the customer, with the aim of implementing the lockout-tagout procedure in all areas of the plant. The purpose of the LOTO approach is to implement the practices and procedures necessary to disable machinery or equipment, thereby preventing the release of hazardous energy, while employees perform servicing or maintenance activities. Such unintended release of hazardous energy can result accidents and serious injuries, or even death.
“Lockout-tagout is about minimizing the risk for accidents in the workplace. By switching off the energy sources and locking them with padlocks, as well as clearly marking this machine as being worked on, our employees can safely perform maintenance work”, says Benita Padam, Quant maintenance engineer in Ludvika.
Safer working environment and reduced costs
She highlights several advantages of implementing lockout-tagout on the site. Mainly from a safety point of view – but there are also several other positive effects.
“It becomes clearer who is responsible for doing what and how a job should be carried out. In addition, maintenance work becomes more efficient, leading to reduced costs when the machine is not out of use longer than necessary.”
Jens Langörgen, Quant site manager in Ludvika, is also very positive about the implementation of lockout-tagout:
“This is a particularly important safety project to provide greater understanding and knowledge on issues related to safe maintenance stops, to reduce the risk of accidents and incidents.”
The project is now just over halfway through. In five of the site’s nine areas, implementation is complete, while work is ongoing on the remaining four areas. It is a large project where the biggest areas have several hundred machines to be checked.
“The customer provides us with a list of all the machines for each area. Together with a maintenance technician, I go through the list to sort out where we need to implement lockout-tagout”, Benita explains.
“When the work starts, we go out to all the machines on the list and review what processes there are for every machine. We document and take pictures of them, and then I create a lockout-tagout instruction for each machine.”
Safety is, of course, a top priority of the project. Therefore, when the instruction is complete, it is given to another maintenance technician who has not previously been involved in the work. The maintenance technician follows the instructions for each machine, to verify that it is correct.
“Incredible improvement in communication with the customer”
The finished instructions are collected at a lockout-tagout station. In addition to the instructions, there is a cabinet with all the locks used during maintenance work, as well as a sign that clearly marks the station.
“The locking cabinet itself is locked with a padlock, the key to which is in a box that opens with a code. The box is opened by the customer’s contact persons, since the idea is that every work we do, will start with a handover between Hitachi ABB Power Grids and Quant”, says Benita.
“The customer makes a written handover to us before we start working, and then when the work is done, we make a handover back to them and tell them how it went.”
She thinks that the process with handovers from and to Hitachi ABB Power Grid’s contact persons has strengthened the customer relationship and increased communication.
“It works very well since we agree with the customer on a suitable time, so that we can meet at the station and do the handover. There has been an incredible improvement in communication between us.”
The customer has also given positive feedback on the project.
“Absolutely, they think it works very well. This makes it easier for them as well, that they know what jobs are ongoing when we are there, which of course makes their planning easier. Communication is key, we have a very good dialogue”, says Benita.
Major safety focus
The implementation of lockout-tagout on the site has taken place area by area. After the instructions for each area have been written, verified, and collected at the lockout-tagout station, training with the relevant contact persons at Hitachi ABB Power Grids is held.
“I explain what lockout-tagout is, how this process should be carried out and what the benefits are. We always conduct at least two trainings for each department, but sometimes we have additional ones if someone is sick, are working shifts or similar, since it is important that everyone gets the information.”
Trainings are also carried out with Quant employees to ensure that knowledge is kept up to date and to maintain a good safety culture.
“We have repeat trainings in for example risk assessments and lockout-tagout. We do this to ensure that everyone can feel safe at work and it is a good reminder of why we do these things every day”, says Benita.
She is supported by Jens, who highlights the importance of working safely.
“Working systematically with occupational health, including electrical safety, is highly prioritized at Quant. We are proud to be able to take responsibility for lockout-tagout from start to finish, in close cooperation with the customer and its employees.”
“To me, it is essential that we can ensure good routines for a safe disconnection of energy, with clear instructions for all employees. We should always work safely so that everyone can go home healthy and unharmed after the working day, for which this lockout-tagout project really contributes.”
Benita Padam, Quant maintenance engineer