febrero 24, 2021
Improving reliability and efficiency with Quant’s digital tools
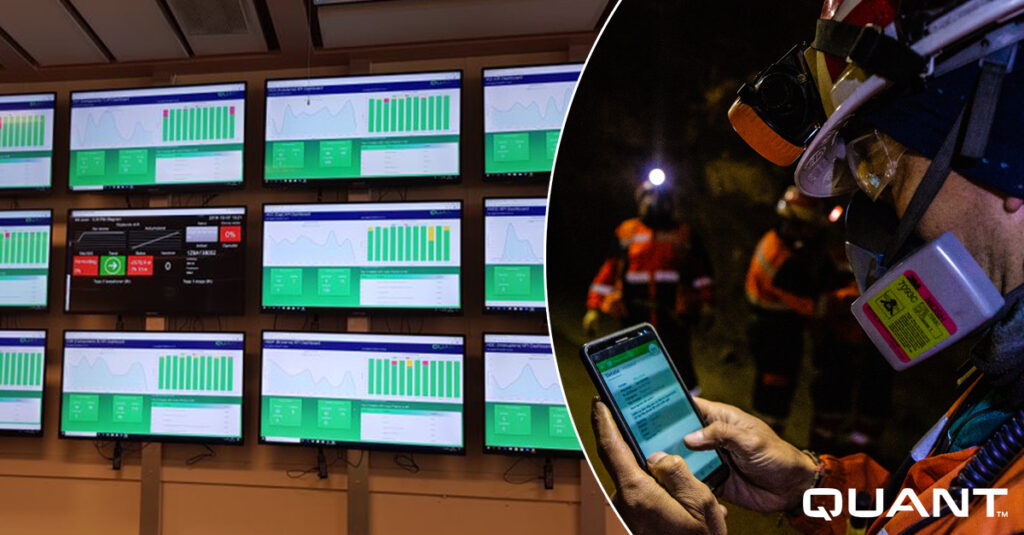
Digitalization is a key area for Quant. Through smart services, we strive to generate outstanding customer value and help our customers improve plant performance. quantWorx suite is a set of digital tools used at our customers’ sites to assist in delivering world class maintenance.
In 2020, Quant started a digitalization project at one of our sites in Sweden, where quantWorx was implemented to improve the internal process, resulting in increased efficiency and better control of the workload.
We started by visualizing some key KPIs on large screens put up on the wall so that everyone could follow how it is going, which has received very positive feedback from our customers. The visualizations are done using quantWorxDisplay, which shows some common KPIs and work lists using quantWorx data.
Reduced lead times using quantWorxMobile
Another area that was targeted to be digitalized was the way the technicians were receiving and reporting their work. Previously, this was done mainly using printouts of work orders that were handed to the technician when work was to be executed. Using the quantWorxMobile, we are now mainly working digitally on mobile phones where work assigned to the technician can be received, started and reported. This allows us to get a much better overview of what work is ongoing and has reduced our lead times. We also ensure that the work orders are not lost and never reported after the work is done.
– The team on site has been the key to the success of the transformation to become more digital. They were dedicated and willing to adapt their ways to allow the system to support the process, says Robert Berkel, IT Project Manager at Quant.
“A world leader when it comes to maintenance”
Another improvement made during 2020 was when we, together with one of our customers in Chile, started a project with the aim of improving the usage of digital tools. Thus, the implementation of quantWorx meant a great effort by the local engineers to carry out the adaptations in the data structures from the previous CMMS to quantWorx and in turn achieve complete operational continuity in the maintenance service to our client, implementing quantWorx and quantWorxMobile without any interruption in service.
The implementation has resulted in several benefits for the site, improving reliability as well as planning and scheduling.
– I would like to thank the Chilean team for the good work and the excellent contributions they made to the project. A special thanks to the team on site for their patience and understanding. They have made it possible to once again show why Quant is a world leader when it comes to maintenance, says Robert.
Robert Berkel
IT Project Manager
What is your next step to reach the full potential of maintenance? Contact us to learn more!